Процесс промышленного дизайна Rackmount-устройств
Промышленный дизайн не всегда про проектирование диванов, ложек, стульев, бытовой электроники. Дизайн нужен и для rackmount-устройств, а по этой теме информации в свободном доступе практически нет. Крупные студии публикуют много процессов промышленного дизайна, но мало кто из них описывает, с какими проблемами сталкиваются специалисты даже при проработке небольших железных коробок с 2 кнопками и 10 разъемами. В статье я постараюсь рассказать про рутинные задачи и проблемы, с которыми регулярно сталкиваются промышленные дизайнеры.
На данный момент чаще всего я участвую в проработке дизайна либо desktop (прибор на столе), либо rackmount (в 19″ стойку) устройств. У меня также есть опыт промышленного дизайна для кнопочного мобильного телефона, STB + пульт, нескольких программно-аппаратных комплексов. Я заметил, что если 5 лет назад вопрос стоял лишь в функциональности устройства и форма следовала за функцией, но сейчас рынок наполнен, и форм-фактор стал играть значимую роль. Эстетика идет вместе с функциональностью, а не следом за ней.
Сразу хочу отметить, в промышленном дизайне все строже, чем в web. Если в web несоответствие макету на 1px это ерунда, то в промышленном дизайне несоответствие чертежу/модели на 1mm это огромный косяк. Запустить MVP сайта это одна неделя, а запуск промышленного образца от идеи до серверной полки это 6 месяцев. Цикл жизни Rackmount-устройства в среднем 6 лет, как у обычного сервера. Это, конечно, не 30-40 лет эксплуатации, как у автомобиля, но куда больше, чем 1-2 года жизни дизайна сайта.
Как выглядит дорожная карта промышленного дизайна:
Анализ
Типичная задача состоит в дизайне устройства, у которого есть аналоги. Поэтому работа начинается с анализа конструкции аналогичных корпусов и стандартов, которым она должны соответствовать. Выбираются материалы исполнения корпусных деталей. В ТЗ будет указано просто «железо», на практике выбор придет к алюминию и стали. Просто железо очень подвержено ржавчине, мягкое и тяжелое. Его можно улучшить за счет примесей алюминия, кремния, марганца и фосфора + оцинковка и гальванизация. При хорошем раскладе, можно выбрать Д16Т, так как он себя уже хорошо показал в плане баланса прочности и легкости. На резьбу его не советую, а для деталей корпуса — вполне ок. Поэтому стартовые вопросы заказчику всегда:
- Для чего нужен корпус?
- Тираж устройства в первый год?
- Насколько важен дизайн?
- В каких условиях будет работать устройство?
- Кто конкуренты?
Если речь о физико-механике и нет высоких требований к температурным режимам, то можно заменить пластиком, всякие фторопласт/тефлон/капролон/стеклонаполненный полиамид или PVC-U, PP-H, PPN. На уровне дизайна создается куча эскизных зарисовок, поиск идей по открыванию крышек корпуса, что является по сути обычной практикой дизайн-мышления. Динамичные и современные формы в стиле Карим Рашида рисовать бессмысленно, поскольку речь идет об оборудовании для серверных шкафов. Вас ждет монтажная единица 1U. Корпус высотой 1U с возможностью установки в телекоммуникационный шкаф 19”.
Если устройство очень сложное, то сначала конструкторы прорабатывают узлы, механики, реализацию функций, и только после этого дизайнер придает эстетическую форму и UX. Все это этап R&D, длится суммарно 4-8 недель. Общий процесс любой детали выглядит так: задача ➝ дизайн ➝ инжиниринг + физический дизайн (синтез и топология) ➝ документация ➝ прототип ➝ тестовая партия ➝ серийное производство. Есть подшаги, такие как RTL дизайн, Mbist, FGPA, РСВ.
Проработанные концепты показываются заказчику. Появляется одно направление для развития или несколько, это тоже нормальная ситуация. Сразу же подключаются инженеры, поскольку разработка своего корпуса потребует сертификацию на соответствие ТР ТС: электромагнитная совместимость и безопасность при работе с 220В. При заказе готового шасси корпуса производитель берет сертификацию на себя, но не всегда, так как сертификацию на соответствие ЭМС и электробезопасности проходит не корпус, а изделие целиком. ЭМС промышленного класса по МЭК 61000-6-5:2001. Сам корпус не является источником помех, поскольку внешние помехи не влияют на его функциональные качества. С электробезопасностью то же самое. На рынке есть СВЧ-лаборатории, которые помогут исследовать уровень электромагнитных помех.
Но готовое шасси это и ограничения. Всегда старайтесь заложить блоков питания и вентиляторов с запасом, они постоянно ломаются. И закладывайте размер шасси на 7 лет вперед. Чем больше портов, тем больше устройств можно подключить. И в современном мире обязано быть питание через Ethernet (PoE) — всякие камеры, IP-телефоны, точки доступа WiFI.
Так, для сетевого оборудования готовое шасси это классное решение, особенно если сеть не особо распределена, немного стоек. Шасси при одинаковой портовой емкости дешевле и оно будет служить до 10 лет. Можно вставить разные линейные карты для конфигурации портов, обычно это 2-4-8-10-12 карт расширения.
Отдельной сертификации потребует электроника. Еще до начала производства. Для базовой электроники нужен сертификат электробезопасности. Если добавляется WiFi, то еще и радиобезопасность (FCC). Эту задачу можно делегировать производству в Китае, но это платная услуга.
Вполне нормально по результатам обсуждения выбрать уже готовый корпус с минимальной доработкой передней, задней панелей и внутри. Многие компании подгоняют микросхемы под серийные корпуса. На рынке достаточно стандартных корпусов электротехнического назначения в исполнении IP65 или более защищенных, учтены искробезопасность, взрывобезопасность, накопление поверхностного заряда. В таком случае работа дизайнера сводится к UX эргономики и работы устройства в среде, расстановке цветовых акцентов. Но это тоже сложная работа, завязанная на функции. Например, на серебряном цвете всегда видны все огрехи корпуса. Палевые цвета, белая ночь, существует много красивых оттенков для работы. Хотя гайдлайны часто регламентируют все делать в цветах: черный, белый, серый, зеленый, синий, которые отвечают на 90% всех предпочтений. Но можно сделать и свой корпус из сплава алюминия (АК12оч, GALSI13). Встречаются корпуса и из магниевого сплава, AZ91. Магний весьма легкий материал, именно из него делают клише.
За такую простоту мы должны сказать спасибо Алану Тьюрингу, именно он заложил идею, по которой одинаковая микросхема может быть и в компьютере, и в стиральной машине.
Разработка грубого 3D-эскиза и согласование предлагаемой компоновки
Вы удивитесь, как много всего можно сделать с помощью картонной коробки, термоклея и маскирующей ленты. Делаем физические макеты в реальном масштабе, начинаем продумывать конструкцию и детали. В здоровом процессе работы вы закладываете дизайн-язык, то есть, какие элементы будут изюминкой устройства. И скетчи, много эскизов.
Компановка внутри корпуса с учетом необходимого набора внутренних компонентов (платы, источники питания и пр.), а также требований к конструкции: на этом этапе решается, как будет открываться корпус (сдвиг-подъем).
Начинается проработка активной системы охлаждения, и это одна из важнейших частей работы. Вентиляторы, охлаждение свободным потоком, радиаторы, «горячая смена» вентиляторов и блоков питания. Но могут резко прилететь требования про безвентиляторный дизайн. В rackmount принято монтировать два блока питания, в случае выявления стабильного снижения уровня батареи ниже требуемого будет выполнен переход на другой элемент питания + индикация работающих блоков питания. Дело в том, что температура окружающей среды работы устройства от -40 до 85 °C, со снеговой нагрузкой и прочими радостями эксплуатации промышленного оборудования, и устройство должно быть готово к любым ситуациям. Для подключения резервного источника питания должен быть выделен отдельный разъем, и уж точно не USB (в Industrial за такое бьют). Все начинающие специалисты сталкиваются с ситуацией, когда из-за плохих кабелей/батареек система зависала, и команда тратила неделю на поиск проблемы с софте. В самом простом случае, питание подается через интернет-кабель (PoE), по стандарту 2009 года 802.3at, 25.5 Watts DC Power.
По 3D-модели сразу должно быть понятно, какого типа будет охлаждение, например, front to back (спереди холодный воздух затягивается, сзади выходит горячий). Это бывает указано в изначальных требованиях, т.к. часто зависит от устройства серверной у заказчика. Либо, со стороны портов вентилятор забирает воздух и выдувает назад, от этого зависит расположение устройства в стойке. При этом, описанного в ТЗ заказчика охлаждения почти всегда не хватит на практике, поскольку лазерам нравится прохлада. Для них добавляется воздуховод. Я еще люблю делать перекрытия из упругого материала с вертикальными разрезами внизу, получается своеобразная «бахрома». Данная бахрома позволить проложить кабели как угодно, но при этом будет перекрывать путь воздуху. И в конце кто-то может добавить картонку перед потоком холодного воздуха, проводя аналогию с автомобильным радиатором — не надо так.
Если нужно использовать магниты, например для скрепления ручки и доски, то у меня всегда под рукой неодимовые магниты. Ферритовые магниты дают меньшую жесткость, и быстрее размагничиваются.
С другой стороны, если устройство будет стоять в кабинете топ-менеджмента, блок питания должен быть тихий, и мы используем пассивное охлаждение. Тогда у вас будет возможность литья корпуса из пластмассы или вариант с изготовлением корпуса на 3D-принтере, проблем станет меньше. Литье пластмасс под давлением это очень дешево в производстве, но изготовление пресс-формы может обойтись в сотни тысяч рублей. Существует вариант пресс-форм из силикона, если нужно бюджетно и материал это пластик или резина.
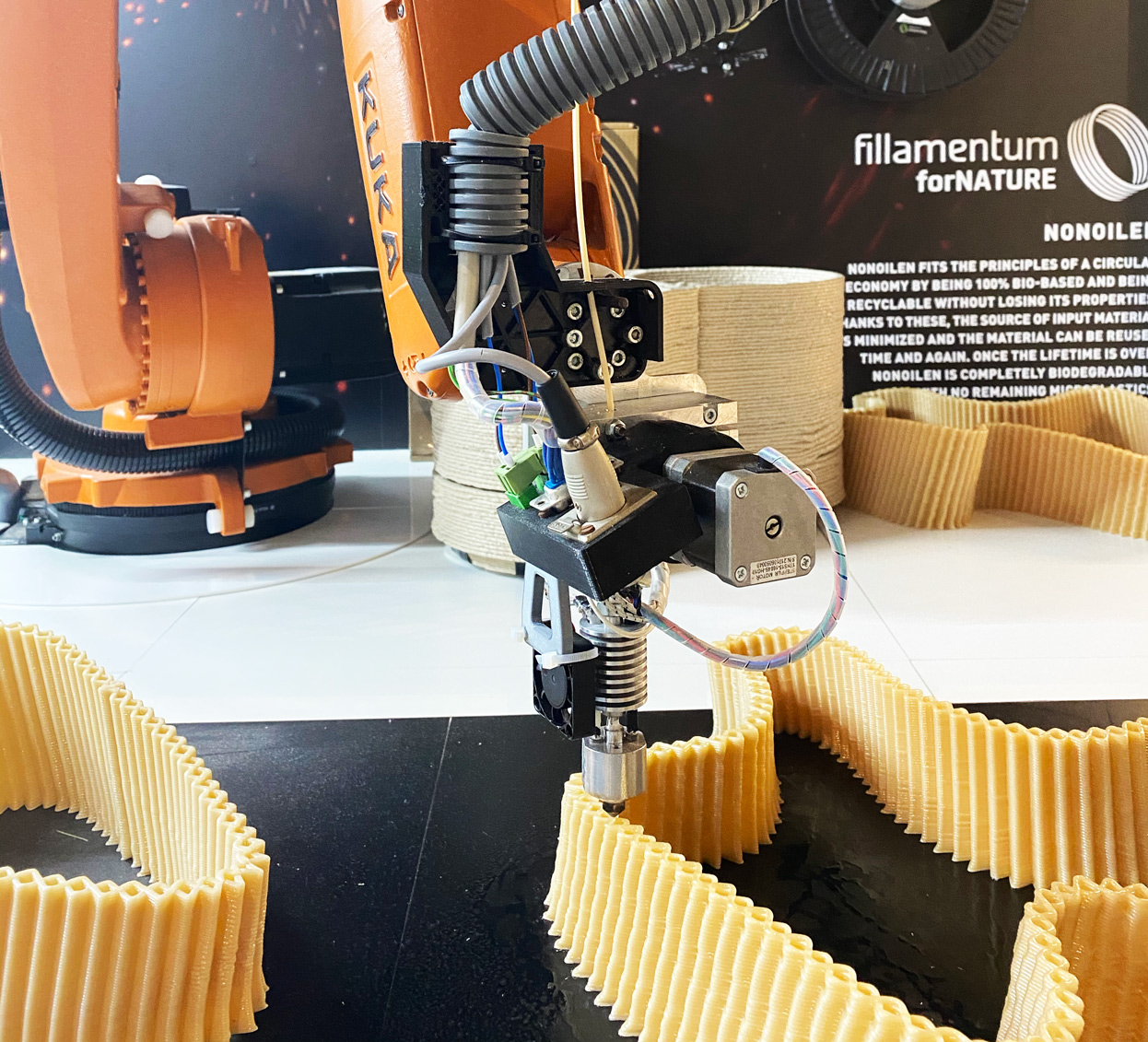
Любое изделие может соответствовать двум из трех критериев: производительно, дешево, надежно. Если мы хотим корпус из железа с минимальным бюджетом, то и материал будет жесть.
На данном этапе важно понимать, будет ли ЖК экран на передней панели. Будет ли это ЖК экран с текущим состоянием переключателя, или это полноценный сенсорный экран с графикой, который заменит физические кнопки? Второе резко усложняет задачу. Но в таком случае часть механических кнопок можно заменить на программные. Это уменьшит стоимость, сделает инжереную реализацию проще. От этого зависит размещение механических кнопок и переключателей, и проработка их дефолтного состояния. И какая будет примерная масса. А вдруг нужен микрофон? Выбрали ленточный, а он провис.
Работа ведется в Alias, Rhino, Siemens NX или SolidWorks, никаких 3ds Max, Maya, Cinema. В самом крайнем случае, для работы с формой можно использовать AutodeskSpeedForm и Autodesk Surface, особенно если ваш предшественник не читал эту статью и отдал вам работу в 3ds Max. Причем Alias и Rhino считаются в большей степени дизайнерскими, концептуальными инструментами, тогда как SolidWorks это полноценная CAD-система. Есть вероятность встретить софт вроде Altium designer и Creo. По результатам итерации создается драфтовая модель, и идет повторная презентация визуализации в реальной среде. На рендере показываем глянцевость материалов и цвет. Но реальное разнообразие задач для софта способно удивить юного эксперта: подсчет аэродинамики, механических и тепловых нагрузок, магнитные поля и электроавтоматика. Поэтому и связка получается вроде SolidWorks + Flow Simulation + Simulation + Motion. Или ANSYS с CFD-пакетами SigmaFlow. Ну и если совсем денег не жалко, то CATIA с модулями, Alias и Icem Surf.
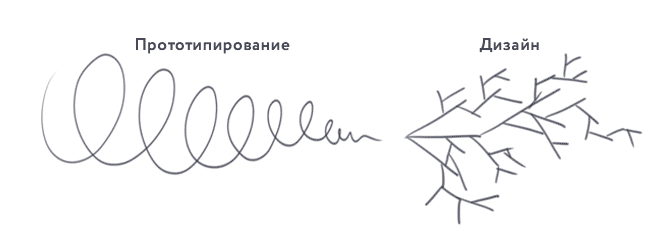
Дизайн можно разбить на следующие этапы: эскизы ➝ детальные эскизы ➝ 3D ➝ визуализация ➝ 3D-принтер.
Некоторые детали сказываются на восприятии устройства. Так, когда смартфон вибрирует, в нем вращается на небольшом моторчике смещенный в сторону груз. Это можно потестировать только вставив такой моторчик и руками ощутить результат.
Проработка деталей
Создаете mood board. Это работа с цветом, подбираем оттенки материалов (силикон, пластик). Уже нужно быть готовым выдать готовые CAD модели. Важно проработать положение не только кнопки «Питание», но и «Восстановление заводских настроек», которая обычно монтируется на плату.
Самому делать продукт не надо, но нужно понимать, как он будет производиться. Если для веб-дизайна важно понимать HTML/CSS/JS, то для промышленного дизайна нужно получить опыт работы на:
- 3-Х сегментальный листогиб
- гибочный ЧПУ
- Фрезерный станок
- Лазерный станок (макетирование корпусов, в идеале Diamond Turning с 5-10 микрон точностью допуска)
- Пресс (с инструментом)
- Ручные сварочные клещи
- Один из многофункциональных инструментов
- Сверлильный станок
Расходники и survival kit:
- Набор торцевых головок и бит с трещоткой
- Набор плашек и метчиков
- Тиски с винтовым креплением и все размеры ключей
- Поворотные детали
- Компрессор
- Динамометрическая отвертка
- Цифровой штантгенциркуль
- Этикет-лента для записей на девайсе
- Радиомонтажная лупа, флюс-гель, пинцет, кусачки, стеклотекстолит,
Весь этот набор инструментов вам понадобится для прототипирования, но работать над макетным образцом будет вся команда, не только вы. Это сварщик, два слесаря, электромонтажник, программист PLС. Если повезет, то сможете многое сделать на 3D-принтере. Если не повезет, то добро пожаловать в мир пенополистирола. Инженер-конструктор будет вам помогать переработать идею в технический смысл.
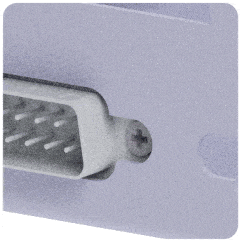
Зачем такие сложные инструменты? Если есть требование, чтобы съемная часть корпуса после удаления крепежных элементов требовала усилия на сдвиг перед подъемом, то спрототипировать это пластилином или лего не выйдет, только тяжелыми материалами. Для внешних соединений деталей корпуса, за исключением крышки, можно использовать неразъёмный или антивандальный крепеж и попробовать взломать. Ход микропереключателей не должен допускать образование щели при открытии части корпуса до срабатывания сигнала о вскрытии, это всегда весело тестировать. При прототипировании сдвигаемых частей корпуса важно, чтобы съемная, сдвигаемая часть корпуса заползала под отгибы для исключения возможности подсунуть под крышку плоский предмет.
Например, при производстве чугунной детали на заводе, придется пройти следующие этапы:
- Чертеж литейной оснастки.
- Изготовление формочки (литейной оснастки). На каком-нибудь Sinto FBO-V.
- Шихта. Этап разгрузки материала и проверки, проверка на ГОСТ.
- Плавка.
- Производство форм на формовочной машине.
- Заливка металла в форму.
- Очистка и проверка на соответствие чертежам.
Довольно сложно и долго. Так что, для проверки дизайна изделия и удобства собираемости можно смело брать 3D-печать или фрезеровку. 3D-печать берем самую дешевую, пластиковой нитью, или FDM. Если ресурсы позволяют, то более дорогие SLA или SLS можно даже показать клиентам.
Если же прототип пойдет в эксплуатацию, то это уже фрезеровка и литьё полиуретана. Фрезеровка пластика или металла это почти финальный прототип, с качеством финального продукта. Кустарные способы тоже допустимы: нужно соединить две детали? Легко, берете любую железку и приваривайте. Дело на 5 минут. На этом этапе должны окончательно сформироваться габариты изделия. Они могут отличаться от изначальной задумки, так, у колонок есть акустический объем, который не позволяет сделать устройства меньше определенных габаритов. Для гибких деталей подойдет литьё в силикон.
Итого, технологии прототипирования:
Дешево:
1) Из палок, пластилина, пенопласта, глины, коробок, и прочих легко обрабатываемых материалов. Нужны для оценки внешнего вида и базовой эргономики.
2) Печать пластиковой нитью (FDM). Требуют доработку напильником, покраску, финиширование. Годятся для анализа внешнего вида, эргономики и веса изделия.
Приемлемо (1-10k рублей):
1) SLA, SLS, лазерное спекание, печать фотополимером. Годится для проверки собираемости изделия. Но результат хрупкий, и кнопки при нажимании будут ломаться.
Дорого (10-30k рублей):
1) Многоосная фрезеровка пластика и металла. Материалы из серийного производства, а значит и прототип очень приближен к реальному.
2) Литьё полиуретана в силиконовые формы. Мой любимый вариант, такие прототипы сразу показывают жесткость, цвет, фактуру, можно заложить резину и прозрачность, поведение на морозе и жаре, электрические свойства.
3) Литье пластика под давлением в легко-обрабатываемые формы. Малое тиражное производство финального образца изделия.
Моделирование теплового режима корпуса
Ваши основные проблемы это перегрев устройства и бесперебойность питания, от этого пляшут все решения. Нужно осознать боль: корпус с отверстиями обеспечивает лучший отвод тепла от компонентов при нормальной окружающей температуре, что важно при работе на границе допустимого диапазона температур. Нормальным решением будет закрыть отверстия мелкой сеткой. И при этом обеспечивать невозможность доступа (путем подключения проводов и т.п.) к элементам материнской платы, ножкам данных элементов и отладочным разъемам платы. Важно тестировать процессор на максимальной нагрузке, для проверки шасси на теплоотвод. Особенно, если это FPGA. Если процессор в районе Allwinner R18, Amlogic S905 или Allwinner A64, то вам еще повезло. А может быть и самый дешевый RISC-V, который пусть 64-битный и интереснее ARM по архитектуре, но требует досконального тестирования в силу новизны. Китайцы уже используют RISC-V даже в ноутбуках.
Решаем, нужно ли делать заглушки для неиспользуемых плат расширения. Какие стенки будут перфорированными. Если есть опасность попадания воды, то прорабатывается защита корпуса от проникновения воды и посторонних предметов, соответствие степени защиты IP30 по ГОСТ 14254-96.
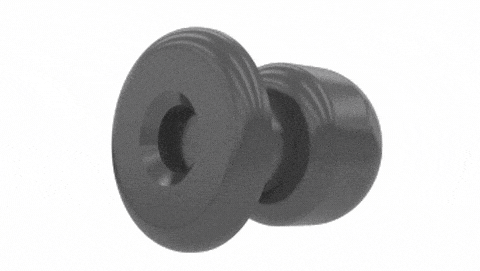
Корректировка 3D-моделей
Изучаем, какой графический интерфейс может понадобиться, работаем над графикой дисплея. Минимизируем количество съемных частей корпуса с крепежными элементами, доступными снаружи. В идеале должно быть 2 части: основание и крышка. Как говорил Дитером Рамс: «хороший дизайн настолько мал, насколько это возможно». Каждая съемная часть корпуса должна фиксироваться минимум двумя микропереключателями, подключенных последовательно в кольцо. Срабатывание любого приводит к сигналу о вскрытии. Меньше деталей корпуса=меньше микропереключателей.
Это также позволит корпусу убрать отверстия, позволяющие получить доступ к внутренним компонентам изделия посредством прямого щупа. Когда с корпусом становится все понятно и прототип устраивает команду, делается заказ заводам на тестовые изделия (5-10 экземпляров). С пометкой EVT, соответствие финальном продукту и по виду, и по работоспособности.
На этом этапе можно поиграться с краской. Так как корпус металлический, мы наносим эмаль. Эмаль это полностью паронепроницаемое покрытие, содержит оксиды щелочных металлов, кварц, цветные пигменты, и антикоррозионные пигменты для лучшей защиты металла. Это не интерьерные эмалевые краски! Например, полиуретановая эмаль используется для обработки железных инструментов, чтобы у людей на севере инструменты не примерзали к рукам.
Весьма хорошая технология для украшения металлического корпуса это гальваническое покрытие. Его можно применять как на огромные, так и на маленькие объекты. Это может быть покрытие медью, цинком, никелем, латунью, золотом, серебром. Есть где разгуляться, каждый вид покрытия добавляет разные полезные характеристики.
Реализация корпусов подрядчиками обычно хромает на обе ноги. Если в чертежах указан радиус скругления 1mm, то с производства могут прийти радиусы скругления более 2 мм, и углы будут выделяться. Самый распространенный косяк это неровные прилегания крышек и кривой монтаж разъемов, причем, если по чертежу допустимый зазор 0,2-0,4mm, то на практике зазор может быть и 3mm. Каверны и вмятины тоже обычное дело. Ваша задача — получить EVT-образец продукта (Engineering Verification Test) и тщательно проверить.
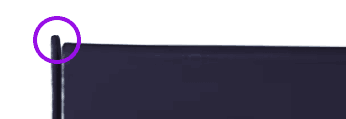
Основная задача на этапе проверки тестовых устройств с завода состоит в отслеживании косметических недостатков, не влияющих на функционирование изделия. Помимо осмотра корпуса, имеет смысл посмотреть и на микросхемы. Текстолит должен придавать плате хорошую жесткость. Компоненты тоже могут стоять криво, даже те, которые ставятся в отверстия/разъемы. Платы могут быть с остатками флюса. Существует стандарт IPC-A-610-E на отмывку флюса, по которому видимые остатки удаляемых флюсов или остатки любых активных флюсов являются дефектом для всех классов 1,2,3.
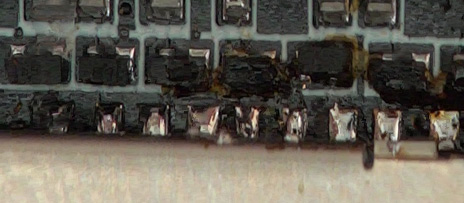
Одна из важных задач это понять, насколько удобно ремонтировать устройство. Неаккуратность при работе со стопорящей жидкостью для стопорение крепежных винтов приводит к попаданию жидкости на компоненты и поверхности деталей, находящихся рядом с винтами. Это не только затрудняет разборку изделия (ухудшает ремонтопригодность), но и может оказать неблагоприятное воздействие на компоненты в связи с химическим составом стопорящей жидкости. Ремонтопригодность и удобство работы сильно зависит от трассировки кабелей внутри корпуса. В 3D-компоновку добавляется дополненная модель соединительных кабелей. Прорабатываются места для установки микропереключателей для контроля вскрытия корпуса, заглушки на разъемы.
Даже самые простые вопросы, вроде выбора батареек, имеют свои подводные камни. Так как эксплуатация устройств происходит в экстремальный условиях, батарейки для массовых типов (consumer grade) с ограничением в +60°С не подойдут. Познакомитесь с батарейками для специальных типов (industrial grade): +70°С, +80°С, +85°С, +125°С. И замена батарейки должна проводиться без вскрытия корпуса устройства, что подразумевает наличие люка для смены батарейки. И после этого мы получаем наш DVT-образец, который практически идентичен серийному образцу. Не забываем и про софтверную часть. Так, любой промышленный ПЛК идет с картой уровней на случай аварии. Любой сбой должен триггерить установку безопасных уровней на выходах. Говоря об экстремальных условиях эксплуатации, подсчет может быть методом конечных элементов в openFoam.
Более экстремальные условия, чем в Арктике и Космосе, придумать сложно. Как минимум, работе электроники мешают радиационные пояса в плоскости магнитного экватора. Часть заряженных частиц выпадает на полюсах, где сходятся магнитные линии. Это приводит к северному/южному полярному сиянию. Явление красивое, но это космическая радиация.
Заряженные частицы атакуют полюса, поэтому в этих широтах самолеты не часто летают. Нас на земле защищает атммосфера, а на высоте 10км появляются высокие дозы радиации, которые копятся пилотами. Чем выше — тем больше облучение. Для электроники это значит побольше экранирования.
Другая частая проблема это водно-солевой туман. Корпус нужно обрабатывать методом химической конверсии, и протестировать по военным стандартам MIL-STD-810 и RN6-ASTM D610.
Если заказывалась антенна, то самое время понять, дотянется ли она до точки назначения. И самое главное — где эта самая точка назначения. Антенна это колебательный контур. В самом понятном случае точка назначения расположена в космосе. Передача сигнала в космос требует огромной антенны в виде полусферы, которая направлена вверх. Это направленная антенна, которая бьет довольно далеко, но мы не можем отправить сигнал больше, чем энергия сигнала. Для увеличения дальности передачи сигнала, энергия концентрируется. Чем более «узкий» отпраляемый сигнал, тем больше коэффициент усиления антенны. Самые слабенькие антенны бьют на 360°, параболическая антенна значимо мощнее. И самая мощная антенна — Яги. Такие антенны можно увидеть на государтсвенных учреждениях, такая антенна способна подогреть вашу мокрую одежду своим сигналом. Они, как и многие другие антенны, могут быть горизонтальной или вертикальной поляризации. И для совсем взрослых — загоризонтный радиолокатор. Чем больше препятствий на пути следования сигнала, тем меньше шансов, что сигнал дойдет до получается, решается увеличением частоты сигнала. Сигнал летит от отправителя (MQTT-сервер, или что то более старое на OPS) до получается по зона Френеля, т.е. волна распределяется от точки к точке не по прямой линии, а изгибается.
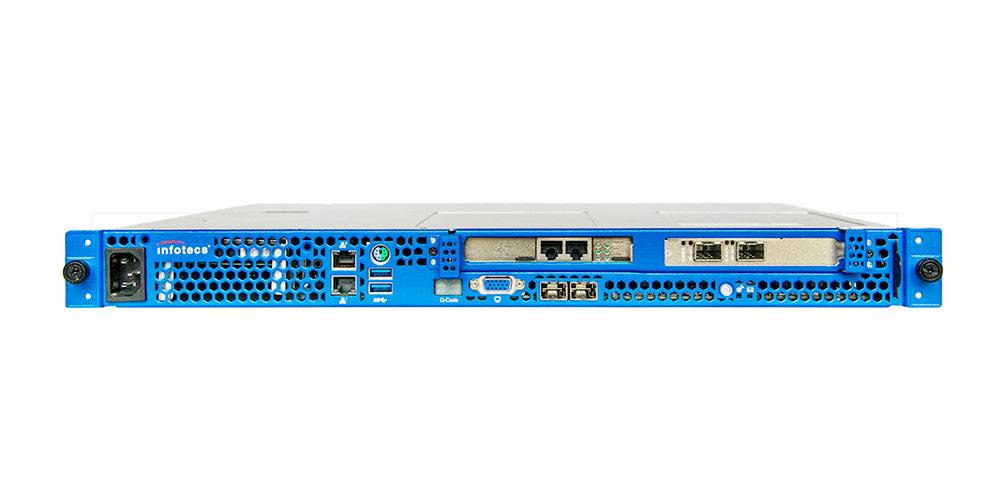
Разработка упаковочной тары
Окончательное утверждение маркировки + шильдов с указанием наименования изделия, его обозначения, серийного номера и даты изготовления. Маркировка тары должна производиться по ГОСТ 30668-2000. Тара обычно разовая индивидуальная и крупная, т.к. миниатюризация это скорее из области IoT/IIoT. На тару есть ГОСТ, 23088-80. В тару добавляется этикетка, упакованная в пакет из полиэтиленовой пленки.
Основное, что важно учесть при разработке тары, это транспартировка и хранение. Для сетевого промышленного оборудования это соответствие условиям «С» по ГОСТ 23216-78. Транспартировка таких устройств производится в отапливаемых герметизированных отсеках, причем не важно, в грузовом автомобиле с пневмоподвеской, поезде или самолете. Хранение устройств происходит в складских помещениях в штатной упаковке при температуре окружающего воздуха от -40 до 60 oС и относительной влажности до 95 % (без выпадения конденсата и образования инея).
По маркировке работы не много, в общем случае надо отследить, чтобы все разъемы и элементы индикации изделия имели правильную маркировку. Имеет смысл соответствовать ГОСТ 18620-86 (Изделия электротехнические. Маркировка) и не забывать про манипуляционные знаки ГОСТ 14192-96.
По маркировке будет также много косяков со стороны производителей, куда больше, чем в обычных типографиях. Косяки бывают на уровне изменения логотипа с цветного на черно-белый. О попадании в цвет даже говорить не приходится. Почти наверняка заказы будут разбросаны по нескольким типографиям, поэтому очень желательна цветопроба и разослать в типографии эталонные цвета.
По итогу считаем финальную MSRP.
Подготовка комплекта данных для финального производства
Данный этап носит аббревиатуру PVT, пробная партия. Для контроля приходится самостоятельно выходить на завод, который не будет хотеть работать без посредников. Нет никакой разницы, где завод расположен: Россия, Китай или Европа, косячат все. Завод должен принять на вход файл .step или .iges), тираж, требования, и после переговоров вы ожидаете мастер-модель и формы для производства.
Когда тестовые устройства с завода проверены, настало время размещения заказа контрактнику на полное производство. Будет много инженерных штук, вроде установки BIOS, заливки ПО, но на этом этапе вы пойдете верстать инструкцию к устройству, что уже не относится к теме промышленного дизайна.
Может ли всю эту работу сделать инженер вместо дизайнера? Да. Но результат будет такой же, если Back-end разработчик напишет сайт на Bootstrap без дизайна. Вроде работает, но UX плохой. Аналогично, инженер пройдется по IPC-A-610E и выпустит продукт, который создаст много проблем всем специалистам, работающим по всей бизнес-цепочке. Промышленный дизайнер при работе над rackmount-устройствами сможет найти баланс соответствия всем требованиям и комфортом работы. А возможно, и привнести инновации.
40 комментариев
Иван Пегашев
Как рассчитать тепловыделение?
Цветков Максим
Сначала идет прикидка приблизительно и умозрительно (это не сложно, если корпус фрезерованный), потом расчет ведется в САПР типа ANSYS. Специально обученными людьми.
Anastasia Biryukova
Как принято, да и принято ли, защищать платы и укреплять разъемы для увеличения надежности?
Цветков Максим
Если вопрос только в надежности, то для соединения плат между собой можно использовать цанговые разъемы, что бы обеспечить надежный долговременный контакт разъемных соединений. Также, обычно платы покрывают лаком и специальной диэлектрической смазкой, т.к. в экстремальных условиях будут проблемы с повышенной влажностью, что чревато окислениями и даже наростами.
Анатолий
Здравствуйте, есть ли практики добавления брони в устройства для экстремальных условий эксплуатации, и при этом сохранении эстетики корпусов?
Цветков Максим
Броня обычно располагается под обшивкой, и это плоский стальной лист. Сталь это прочный материал, из стали делают пресс-формы, корпуса кораблей, ледоколов, подлодок. Корпус можно сделать с интересными выпуклыми формами, а под корпусом уже грубая коробка из толстых бронелистов, с правильными углами наклона и распределением нагрузки. Речь, конечно, не об активной броне. Сталь принято использовать для крупных блоков, типа крыши машины. Сплавы (сталь и алюминий) или Кевлар для усиления прочности, или при наличии денег углеродное волокно. Стекловолокно хорошо себя показывает против взрывов, отлично подойдет для укрепления дна машины. Если вес играет роль, то комбинация кевлара и керамические дают эквивалентный уровень прочности в сравнении со сталью.
Вот цвет, который приобретает сталь при закалке определенной температурой. Цвета побежалости. Крайний левый квадратик это сталь без закалки.

Если при закалке использовать специальный полимер, а не обычное масло, можно повысить прочность.
Антон Прошной
Здравствуйте, отличная статья. Да и походу единственная на русском(( подскажите, а как прототипировать более крупные промышленные образцы, по размеру как машина, например?
Цветков Максим
Сложнее, это тема для целого курса) В ВУЗе при прототипировании мы делали простой макет в масштабе, не действующую модель. Но это был бакалавриат, с ограничением по времени на подготовку всех проектных материалов.
В реальном производстве большинство проблем решается на этапе работы в CAD. Если есть косяк на стадии CAD, и на прототип автомобиля нужно добавить водонепроницаемое ограждение на деталь, то для этого:
-делается новая пресс-форма и изготавливается деталь (если деталь сложная, с шиберами, то это сотни тысяч долларов);
-тест детали покажет баги (конденсат падает на резинометаллический шарнир, ускоряя износ) и косяки с допусками, которые +/- 0.01мм, +0.02мм;
-переделать пресс-форму, найти еще баги, переделать пресс-форму, и так по кругу;
-понять, что при сборке на конвейере робот не дотягивается до новой детали и перепроектировать еще пару деталей, так как их отредактировать не получится, ведь их твердость 58 HRC;
-на тесте понять, что шумо- и виброизоляция перестали соответствовать ожиданиям и либо накидать еще материала = увеличивать стоимость девайса (а при серийном производстве увеличение стоимости на 10$ это потери 10 000 000$ при продаже 1 000 000 образцов), либо возвращаться на первый шаг и заново делать пресс-форму;
Ну и куда больше расчетов, вроде прогнозирования трещин на уровне кристаллической решетки, моделирования ползучести и накоплении малоцикловой усталости. Размер + условия эксплуатации: если эксплуатировать машину в минеральной и меловой воде, а машина покрывается грунт-эмалью (бюджетненько продекор 1202), то лет через семь все равно начнет гнить.
Александр Тютюма
А корпуса Apple делаются аналогично? И прочие такие мелкие, но прокаченные по материалам устройства, как материалы влияют на стоимость?
Цветков Максим
Лично я на Foxconn не бывал, но думаю, это литье болванки в виде плит, дофрезеровка + финиширование. Но при тиражах Apple у них доступ к просто потрясающему оборудованию, чего стоят только машины для литографии в крайнем ультрафиолетовом диапазоне (EUV) от ASML Holding NV.
А по ценообразованию, ну на примере часов с сапфировым стеклом и антибликом с двух сторон, стальной корпус и браслетик 316L, водозащита 100 М/10 ATM, хронограф и секундомер, это примерно $400 в магазине. Если циферблат из костей динозавра, то цена растет.
Все небольшие устройства, вроде швейцарских часов, имеют очень широкую вариативность материалов. От углепластиков и низкосортной нержавейки до стали 316L/904L (Rolex), стекла и титана. Это только для корпуса, а стекло покрывается антибликом и может быть оргстеклом с бронепленкой, плексом, хрусталем и сапфиром. Да даже если углубиться в материал корпуса, то это не просто прочная нержавеющая сталь как у шомпола. Apple Watch делаются из алюминия 7000, материал для аэрокосмической промышленности, iPhone 6 из алюминия 6000, Galaxy S9 это алюминий 7003, и хоть все эти материалы не такие прочные, как нержавейка. Из нержавейки делают даже закалочные печи и печи азотирования. Но алюминий более премиальный по ощущениям + дешевле и легче железа (так как он менее плотный = проще и быстрее обрабатывать). А у iPhone X есть нержавейка по краям телефона, это позволяет отполировать поверхность до изначального качества. Первая цифра в номере сплава обозначает серию, алюминий для фольги это 1050 или 1100, банки это 3004 (алюминий + марганец), 6000 это сплав алюминия с кремнием и магнием, а 7000 это смесь с цинком.
Всякие коленочные валы для подлодок это будет сталь 50Г.
Сталь 316L или сплав алюминия AlSi10Mg можно даже печатать 3D-принтером, а вот 904L уже работа ручками на станке. И крупные промышленные объекты, со сталью 40Х, термообработкой 28-32 HRC, и азотированием на принтере не напечатать. Или дюралюминий для лунных аппаратов. Это все тоже влияет на цену, ручная работа всегда дороже.
Бывает и другая крайность: слишком простая noname сталь. Зачастую её делают из отходов, как результат, толщина металла нестабильна и рандомная упругость. Часто закладывают в смету цену на сталь как риск, так как постоянно дорожает.
Известен процесс производства фирменных чехлов Apple: льется очень жесткая поликарбонатная основа 0.6 мм (не TPU), потом покрываем клейким химикатом, и далее покрывает силиконом менее 1 мм. Далее очищает область вокруг кнопок и заливает их. И много-много циклом очистки и ручного труда, далее много слоев покраски (каждый слой добавляет стоимость), и клеится микрофибра на внутреннюю поверхность чехла на станках собственного производства. И вишенка на торте: рисуют лазеров фирменный логотип.
Dima Makn
Мне из интереса для учебного проекта (студент Строгановки), есть эскиз крышки для мотора, по габаритам 350х410х120 мм. Нужно всего несколько штук, материал могу сам раздобыть. Сколько это будет стоить?
Цветков Максим
Такое крупными партиями заказывается, а судя по описанию, деталь под литье. Заниматься фрезеровкой сложных деталей поштучно — цена явно не для студента, но я бы метился в 13-15 000 рублей за штуку. Если конструкция детали правда сложная, то можно распечатать на 3D принтере и допилить, просто загрузите модель на weerg и узнаете стоимость. Но! если захочется дополнительных работ по финишированию детали, а это фрезеровка, галтовка, анодирование, растачивание посадочных под сальники/подшипники, цена может умножиться на 3. Также, отличного качества можно допиться только 3D-принетром, печатая смолой.
Цена еще и от материала зависит, я оценивал по знакомым мне 7075 (В95) и 6082 (Д16Т).
Виктория
Привет! как интервью проводить, если тема очень узкая и я с в ней не разбираюсь? Быстро стать экспертом очень сложно, да и в 20 темах за год экспертом не станешь. Есть какие-либо советы?
Цветков Максим
Поговорите с экспертами из вашей собственной компании, это позволит получить некое представление о теме. Есть ли исследования до интервью? Интервью не обязательно первый способ исследования потребностей. Как раз на исследованиях до интервью можно разобраться в теме на достаточном уровне.
Если вы уже делаете такое интервью и нет времени на все описанное выше, то начинайте интервью с «опишите ваш день из жизни» или «объясните мне, чем вы занимаетесь, как ребенку». Ну и читать книги/статьи, становиться экспертом.
Аня
какими материалами обычно делают интерьеры автомобилей? Спасибо!
Цветков Максим
Обычно пластик с тисненнием под кожу, АБС-пластик (ABS + PC). Скорее вопрос в способе финиширования: soft-touch coated. На алюминий применяют hairline brushed. Можно встретить алькантару (искусственная замша). Говоря о последней, ее репутация испорчена низкокачественными китайскими подделками и самостоятельной обшивкой, но для подлокотника материал отличный.
При этом, алюминий могут применить, только если он выигрывает одновременно и у пластика, и у железа. Алюминий легче железа, но дороже. И очевидно, он дороже пластика, зато долговечнее. Также, он лучше железа проводит электрический ток. Первый автомобиль с полностью алюминиевым кузовом был сделан еще в 1899 году, а сейчас это лишь премиальные авто. В машинах среднего класса из алюминия может быть сделан капот и диски, а крыша и капот еще будут идти без оцинковки. И более тяжелые транспорты, которым нужна прочность и легкость, также могут быть сделаны из алюминия. Для автомобилей, обычно это сплавы серии 5000, 6000, 7000. Если в ТЗ есть закалка, то 5000 отпадает.
Если речь не об отделке, а о самом интерьере, то в первую очередь это сталь и пластик, алюминий и стекловолокно (SUV). Можно встретить и материалы на основе термостабильной, полиэфирной или эпоксидной смолы, это композиты.
Виктор Маргинов Иванович
На производстве в условиях завода можно поставить обычный компьютер, или требуются отдельные виды компьютеров специально для эксплуатации в жестких условиях? Такие как вы в статье описываете, программно-аппаратные комплексы. Спасибо!
Цветков Максим
Зависит от производства, есть специальные промышленные компьютеры для цехов. Они дорогие. Если в цеху стабильная температура воздуха (≈ от +15 °C до +26 °C круглый год), то можно обойтись компьютерами типа Stick (очень компактные), просто спрятать их от пыли в отдельный корпус с кулером для отвода пыли. И оргстекло на монитор, так как пыль на производстве специфичная. Монитор тоже тоже из разряда IDS-3210.
Можно сделать свой собственный компьютер формата miniITX. Охлаждение я бы брал от EKWB, вентиляторы минимум EK-Furious Vardar EVO FF5-120 или другой низкопрофильный кулер на 60мм. Если удастся впихнуть, то JONSBO SHADOW TW4-360 Color.
Julia Shestakova
Добрый день! вопрос наверное не совсем по теме, но темные темы для индустриальных систем — это хорошая или плохая идея?
Цветков Максим
В индустриалке скорее приняты серые темы, а не темные. В давние времена белый цвет выжигал ЭЛТ, и требовали делать темные интерфейсы. Сейчас уже ничего не выжигается, но привычка осталась, и как компромисс — серая тема, которая не выжигает глаза при высокой яркости монитора. Siemens, Emerson даже имеют гайдлайны по рекомендуемым цветам. Стандарт организации ФСК ЕЭС 56947007-25.040.70.101-2011″, 3.3.2.2 Для отображения фона мнемосхем следует использовать цвет: ПТК ЦУС – черный; АСУ ТП ПС – серый.»
И это не хотелки, а требования на уровне стандартов предприятий, хотя по отраслям/вендорам есть отличия. Можно почитать ISO 9241 «Эргономика взаимодействия человек-система», ISO 14915 «Эргономика мультимедийных пользовательских интерфейсов», ГОСТ «Общие эргономические требования». И всем известные ГОСТ Р 52872-2012, руководство WCAG 2.0 от W3C и Section 508, опционально ADA.
Саша Михайлов
Когда задаю материал для производства пластиковых бутылок, это один вид материала или некая комбинация?
Цветков Максим
Этикетка зачастую полипропиленовая, сама бутылка это ПЭТ (полиэтилентерефталат), крышка скорее всего полипропилен (ПП) и полиэтилен низкого давления (ПЭНД). Если бутылка для газировки или косметики, то нужны ударопрочные бимодальные марки полиэтилена высокой плотности (SABIC®HDPE CC254), это прозрачный пластик. Встречается и АБС-пластик. И небезопасный ПВХ.
Victor
Как организовать процесс нормоконтроля на производстве?
Цветков Максим
Работая в CAD-системах, надо соблюдать ЕСКД. Чертежи же потом идут на производство к технологу (в лучшем случае), как и модель STP. Я раньше для этого использовал Компас и T-flex.
Но если работать с гаражным производством над простыми деталями, то строгое соблюдение ЕСКД может нанести больше вреда, чем пользы.
E Kibireva
Привет! интересует тебя создания неудобных обстоятельств для ремонтирования корпуса. Бывает ли обратная ситуация? чтобы для замены деталей вообще не надо было разбирать корпус?
Цветков Максим
Посмотрите, как сделаны Thermaltake p3/p5 и Thermaltake View 28Gb. Для тестировщиков, которым нужно постоянно менять комплектующие в корпусе, очень хорошее решение.
Aliaksandr Valialkin
как происходит анализ конкурентов при создании физических объектов?
Цветков Максим
Анализ конкурентов по технической стороне: нужно посмотреть, удастся ли создать прототип на dev-kit/EvaluationKIT. И экспертно/инженерно оценить.
При наличии бюджета можно купить аналогичные девайсы и разобрать. Если бюджета нет, то есть множество ресурсов в интернете, где устройства разбирают и показывают внутренности.
Alexey Konstant
Как избежать коррозии корпуса у программно-аппаратного комплекса (ПАК)?
Цветков Максим
Если корпус из окрашенной/нержавеющей стали или алюминия, то избежать — никак. Замедлить — использовать антикоррозионную обработку корпуса. Нужна она или нет, тут нужно смотреть на внешние условия, высокая температура и влажность ускоряют коррозию. В пустыне коррозия будет медленной, так как мало влажности, не смотря на высокую температуру. Коррозия скажется не только на внешнем виде, но и на заявленной степени защиты IP. Всегда можно взять за материал корпуса Фиберглас, поликарбонат и АБС-пластик, они не подвержены коррозии.
Я обычно беру старый добрый поликарбонат, он термоустойчивый, огнестойкий, легкий и прочный. Хорошо подходит для мозаичных щитов. Даже использовал монолитный поликарбонат вместо защитного стекла (с заменой после царапин и помутнения). И довольно дорогой склеенный триплекс.
Daria Merckulowa
Привет! небольшие универсальные устройства лучше сделать с какой файловой системой? exfat? sdcardfs?
Цветков Максим
Гугловая Storage Access Framework (SAF). Файлы становятся документами.
Арсений
Привет! хочу начать печатать игрушки для ребенка на 3d-принтере, какие материалы нужно закупить? и вот чтоб дешево
Цветков Максим
Для игрушек подходит PLA.
Запчасти для кухонной техники скорее PETG или нейлон (сложно).
На клее можно экономить, сделав его дома: аптечный энтеродез или PVP К-90 (повидон), и мешаем до полного растворения с изопропанолом или водкой. Пропорция 200мл жидкости на 5гр порошка.
Для нейлона клей БФ-2.
Алиса У
Привет! сколько примерно будет стоить одна корпусная деталь из ABS-пластика? размеры 200х120х90 мм
Цветков Максим
Зависит от сложности деталей, кол-ва отверсий и так далее. Примерно, стоимость прототипа, выполненного фрезеровкой, — $350.
Стоимость одного устройства при производстве тиражом в 25 шт. с учетом формы будет в районе $50.
Тара
Начал проектировать маленькое IoT-устройство, и встал вопрос выбора способа передачи данных и платформу. Есть ли какие-то стандарты, рекомендации?
Цветков Максим
Из платформ могу посоветовать гигантов, таких как IBM Watson IoT, Amazon Web Services, Google Core IoT, Microsoft Azure IoT Hub, ThingsBoard. Отличий между ними довольно мало, разница лишь в экосистеме. И в типе оплаты, где-то за вы платите за каждое устройство, где-то за трафик, где-то за обработку данных.
Мой список вопросов, на которые я должен ответить перед выбором платформы:
1. Каков послужной список поставщика платформы IoT (с точки зрения бизнеса)?
2. Насколько поставщик гибок при адаптации к новым реалиям рынка и технологий?
3. Для каких проектов была развернута платформа и каковы были результаты?
4. Какова дорожная карта у поставщика платформы и совпадает ли она с вашей?
5. Будет ли компания на рынке завтра?
6. Как выглядит экосистема партнеров по каналам сбыта и экосистема вендора в целом?
7. Является ли он частью стабильных экосистем и/или имеет ли он сам хорошие экосистемы?
8. Включает ли его подход к выходу на рынок те сценарии использования, которые вам нужны?
9. Насколько удобна и эффективна платформа IoT для выполнения/включения основных задач?
10. Сколько времени требуется для подключения новых IoT-устройств?
11. Достаточно ли «нулевое вхождение» или на подключение уходит слишком много времени?
12. Работает ли платформа со сторонними системами включения / обеспечения / управления устройствами?
13. Как насчет времени, которое требуется пользователям для выполнения других задач?
14. Насколько удобны интерфейсы и функции, касательно протоколов связи, визуализации, принятия решений, различных приложений в рамках поддерживаемых им сценариев использования?
15. Является ли она открытой, совместимой и удобной для разработчиков платформой?
16. Какие облачные платформы используются? Какие языки программирования?
17. Насколько легко внедряются приложения?
18. Есть ли готовые пакеты данных и функций приложений?
19.Насколько хорошо она связана с бизнесприложениями и другими приложениями IoT, которые вам нужны и необходимы?
20. Поддерживает ли оно надлежащие стандарты, устройства, технологии связи и т. д.?
21. Насколько масштабируема платформа?
22. Учтена ли безопасность?
По сети, обычно коммерческие IoT-устройства отличаются узкой полосой пропускания, сбором данных с низкой повторяемостью. Бывают и исключения, например, видеокамеры. Устройства интернета вещей зачастую работают на LPWAN, что позволяет передавать небольшие объемы данных на большие расстояния. Как общее правило, чем ниже битовая скорость передачи данных, тем на более дальние расстояния можно передать данные. Такая модуляция позволяет передавать данные из подавала на базовую станцию через километры и сквозь множество стен. Чем ниже частота, тем на более дальние расстояния можно передавать данные. Наглядно, 5.8 ГГц это WiFi, а 868 МГц и 433 МГц это простое радиооборудование.
Можно рассмотреть вариант сотовой сети M2M, GSM, 3G+, H+, 4G, и скорость будет быстрая + высокое покрытие, но это не дешево. Для личного устройства ок, для коммерции — не всегда. Либо, если в рамках здания, можно поднять локальную сеть, и тут годятся любые типовые технологии: Wi-Fi, ZeeBee, Bluetooth, но опять же, требуется подавать питание и это не дешево. Ну и предложенный выше LPWAN с протоколом LORA, и мириться с низкой скоростью передачи данных.
Женя Логинов
Как хорошо склеивать пластиковые детали?
Цветков Максим
Под словом «пластик» скрываются разные материалы. Обычно на клее указан тип пластика, для которого клей был сделан. Надо гуглить таблицу выбора основы клея для разных типов пластиков.
Если швы будут подвергаться изгибам — то выбираем контактный клей. Если шов статичный, то выбираем реакционный клей или жидкий состав (без водной основы, только на основе растворителей). Убедитесь, что склеивание проходит в хорошо проветриваемом помещении при правильном температуре, которая также указана на клее. Перчатки, очки и респиратор — ваши друзья, клеи для пластика не безопасны.
Если нужно склеить большую площадь, то выбирайте конструкционные составы и смотрите на тип нагрузок.
Акрид FS22 (ACRID FS22) хорошо подойдет для склеивания большой площади акрилов, стали, алюминия, и даже склеить пластик и стекла. Для ПВХ, либо состряпать дихлорэтан + стружка материала, либо Quilosa SINTEX H44, Cosmofen Plus (специально под окна). Для ПВХ труб есть Bailey L-6023, и «Клей-латка ПВХ» для всяких лодок.
Для ABS-пластика могу порекомендовать цианоакрилатный клей, или универсальный реакционный клей. CUDO сработает за 10 секунд, Cosmoplast 500 даст чуть больше времени. Griffon B-25 даже растворит поверхность, а также опасен для глаз. Еще хорошо себя показали Loctite 406, SikaFast®-555 L05 для автомобильных историй. АБС-пластик сам по себе хрупкий, и шов тоже будет хрупким, лучше его армировать стеклотканями. Либо впаивать проволоку.
Полиуретан — клей Уран. Я им порой ремонтирую обувь. Для полиэтилена подойдет YTAN CLASSIC FIX, Клей Temonten (оставляет постоянную липкую пленку), Аэрозольный 3M 90 Scotch-Weld.